1概况
杭州湾跨海大桥北起浙江嘉兴海盐县,南止宁波慈溪市,全长36km(图1、2)。它的建设将缩短宁波至上海的陆路距离约120km,并彻底改变宁波由交通末端型城市向枢纽型城市转变。

图1 杭州湾跨海大桥地理位置
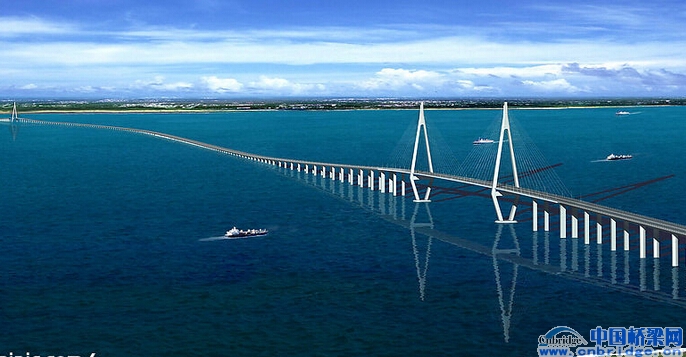
图2 杭州湾跨海大桥效果
杭州湾为典型的喇叭状强潮海湾,桥位处海面宽32km,南岸滩涂长10 km。该区域具有水流、泥沙、海床运动复杂多变,并处于灾害性气候多发地带,桥位处软土覆盖层厚、深埋基岩,南岸滩涂区富集浅层沼气。桥位处最大潮差7.57m,平均潮差4.65m,实测最大流速5.16m/s。实测最大波高4.72m。台风、龙卷风、雷暴及突发性小范围灾害性天气时有发生。由于风、浪、流、潮和雾的影响,全年施工作业日不足180天,建设条件十分复杂。
大桥为双向六车道高速公路标准,桥宽33m,设计速度100km/h;航道桥采用100年设计基准期;桥位区10m高百年一遇10min平均最大风速39.0m/s;北航桥通航孔按3.5万吨级海轮标准设计,通航净空325×47m;南航道桥通航孔按3000吨级海轮标准设计,通航净空125×31m;地震基本烈度为6度。
2.大桥总体设计与桥跨布置
由于海上施工环境恶劣、工程规模浩大和有效作业时间较短,总体设计全面遵循了“预制化、大型化和机械化”、满足百年设计使用寿命要求及设计服从施工等三大设计原则,以尽量减少海上作业,减少施工风险和加快工程进度。同时,大桥平纵线形设计兼顾海域流态分布和航迹线分布,景观上借鉴杭州西湖苏堤 “长桥卧波” 的中国古典建筑设计理念,采用线型优美的大S型平纵线形,最大纵坡3 %。为便于大桥的运营养护、交通组织及抢险救灾,设计上考虑在全桥设置了5处掉头区、1处综合性海中平台及检修通道。
大桥分为北引桥、北航道桥及高墩区引桥、中引桥、南航道桥及高墩区引桥、南深水区引桥、南滩涂区引桥及南陆地区引桥等九大部分。
(1)北航道桥为双塔双索面五跨连续钢箱梁斜拉桥,桥跨布置为70m+160m+448m+160m+70m,总长908m。索塔为混凝土结构,横向呈钻石型,斜拉索采用平行钢丝,扇形布置。索塔处采用钢锚箱。基础采用钻孔灌注桩加高桩承台。过渡墩和辅助墩墩形采用矩形圆倒角断面,承台外周设防撞消能设施(图3、5)。
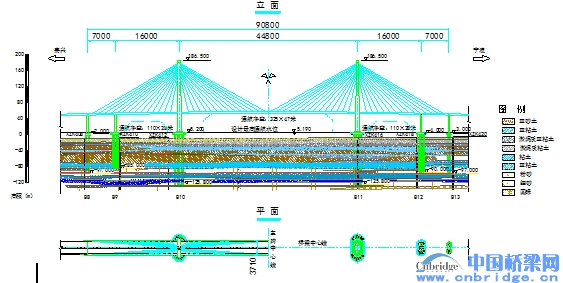
图3航道桥桥型布置
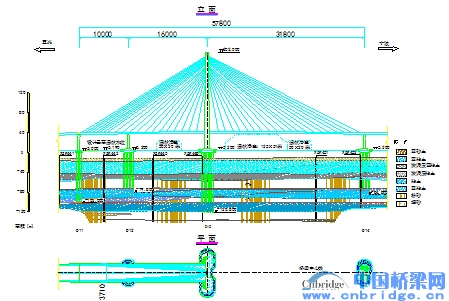
图4 南航道桥桥型布置
(2)南航道桥为独塔双索面三跨连续钢箱梁斜拉桥,桥跨布置为80m+160m+318m,总长558m。主梁、拉索、基础与北航道桥设计基本相同,唯索塔为 “A”型,以利于提高受力性能和结构刚度及抗风稳定性(图4、6)。

图5 北航道桥索塔

图6 南航道桥索塔
(3)与航道桥相邻的高墩区引桥跨径为70m,采用等高斜腹板单箱单室断面。体内预应力管道采用塑料波纹管配合真空压浆。桥墩采用等截面矩形实心墩,双幅整体式矩形承台,钻孔灌注桩基础。
(4)中引134×70m,深水区南引桥86×70m,为跨度70m预应力混凝土连续箱梁(总长18.27km),采用整孔预制、运架一体船运输和吊装;预制桥墩,预制墩混凝土总量约60000 m3,最大吊重440t;基础采用螺旋卷制钢管桩,总用钢量约37万吨。采用大型船机施工和GPS(RTK)测量定位。中引桥基础单幅为9-Ф1.5m钢管桩(图7),南引桥基础单幅为10-Ф1.6m钢管桩。
(5)南滩涂区引桥202×50m,为跨度50m预应力混凝土箱梁(总长10.1km),采用整孔预制、梁上运输和架桥机架梁方案;基础为钻孔桩,用长栈桥法施工。
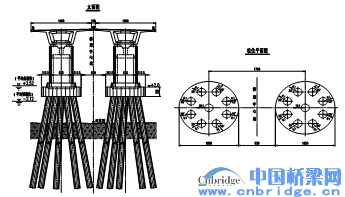
图7中引桥基础9Ф1.5m钢管桩
(6)两岸陆地引起和北滩涂引桥采用跨度30至80m预应力混凝土连续箱梁。北引桥上部结构采用移动模架和悬臂现浇两种工法施工,南引桥采用满堂支架法施工。基础均为钻孔灌注桩。
针对海上各类混凝土结构和钢结构,特别是处于浪溅区和水位变动区的结构,进行了专门的防腐蚀设计,以确保结构的设计使用寿命。
3建桥关键技术
(1)大型构件预制关键技术
1)水中区70m整体预制箱梁
大桥水中区引桥采用70 m先简支后连续的预应力混凝土连续箱梁,总长18.27km,共计箱梁540片(图8),混凝土用量44.8万立方米。预制箱梁为斜腹板箱型截面,顶板宽15.8m,底板宽6.25m,梁高4m,梁重2200t。核心预制技术有:A)整体液压内模系统,模板为分段组拼整体一次性吊装、分段收缩拆除;B)钢筋整体绑扎、整体安装工艺,将梁体钢筋分为底腹板钢筋和桥面钢筋分别设计绑扎和整体吊装入模;C)大体积混凝土箱梁整体浇注技术:对施工组织、模板、预应力体系、灌注工艺、养护工艺等方面进行全面控制,确保梁体施工质量;D)采用塑料波纹管及真空辅助压浆技术;E)在国内首次成功运用预应力混凝土箱梁早期裂缝控制技术。当混凝土达到50%设计强度和50%设计弹模时,对腹板上的部分预应力束施加一定的张拉力(为设计张拉应力的1/3),使箱梁截面上产生一定的均匀压应力,以克服混凝土强度增长阶段的水化热产生的拉应力,从而达到控制箱梁混凝土开裂的目的。
实现了8个制梁台座月制梁30片的生产能力。
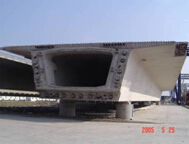
图8 70m预制箱梁
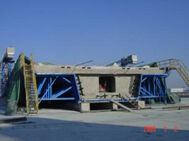
图9 50m预制箱梁
2)南岸滩涂区50m整体预制箱梁
南岸滩涂上部结构采用跨度50m先简支后连续预应力混凝土箱梁,共26联,总长10.1km,共计箱梁404片(图9),最小弯道半径6000m。箱梁顶宽15.8m,底宽6.625m,梁高3.2m,梁重1430t。采用的核心预制技术与70m整体预制箱梁构件基本相同,不同的有:A)采取了高温控制在35±5℃“保温保湿蒸汽养护”措施;B)大吨位预应力混凝土整体箱梁双层存梁施工技术。
实现了6个制梁台座月制梁30片的生产能力。
3) 水中低墩区预制墩身
水中低墩区引桥预制墩身为矩形空心薄壁墩,最大高度17.383m,重440t。预制墩身共有474个,其标准墩墩顶尺寸为6.25m×4.0m。采用的关键技术有:A)内模设计及拼装:墩身内模设计为分节伞形收缩整体内模,直线内模每节高度90cm,变截面内模高100cm。拼装时把内模在平地上撑开,按由下而上的顺序逐层安装。当模板达到高度要求后,微调螺旋撑杆,使模板高度和垂直度的误差在规范允许范围内;B)外模设计及拼装:由于设计从防腐角度考虑,要求取消内部穿锚拉杆,模板支架采用钢桁架。墩身外模由面板、竖向槽钢、横向钢板和支撑桁架组成。待墩身钢筋绑扎完成后,进行外模拼装。和内模一样,外模按照自下而上的顺序拼装;C)钢托架设计:根据墩底外露钢筋长度,墩身预制配套台座(钢托架)设计高度为1.2m,采用钢板及型钢精制。
实现了5个台座月制墩20个的生产能力(图10)。

图10 预制墩身施工
4)水中区螺旋焊缝整体卷制钢管桩
中引桥及南引桥深水区采用钢管桩基础,其规格为Ф1600,Ф1500两类,桩长71~89m,最大单桩重量73t。钢管桩总数量5474根,总用钢量约为3.7万吨。
采用超长不等厚钢管桩的工艺技术。在制造工艺方面解决了不等厚钢板的对接问题,在螺旋焊缝焊接时,采用在线预精焊新技术和强大电流交直流双电源多丝埋弧自动焊新工艺。
钢桩防腐采用以外表涂装为主,涂层与阴极保护联合防护的方式。钢管桩外表采用多层熔融结合环氧复合涂层工艺进行整体防腐。为了增强钢管桩局部刚度,满足防撞和防腐的要求,钢管桩内高程-12m以上填筑混凝土。为此,建造了一条三层外防腐全自动涂敷工艺生产线,解决了表面处理技术、温度控制技术和粉末喷涂技术等三大技术难题。
制管厂三条生产线月平均制桩283根,日制桩最高纪录14根,日涂装最高纪录15根,制桩能力与现场沉桩需求基本平衡。
(2) 大型构件运输及安装技术
1)海上高墩激流区整体预制箱梁架设
在水中低墩区预制箱梁架设施工中采用了“小天鹅”号专用运架船(起吊高度30m)。在高墩区(48m),建造了一艘“天一”号专用运架船,其总长93.40m,船宽40.0m,型深7.0m,设计吃水3.5m。基本性能:运梁时:风力≤8级,流速≤3.5m/s,航速≥8.2节;吊梁作业:风力≤6级,浪高≤2m,流速≤3.5m/s
预制箱梁海上运输及架设主要工序有:专用运架船自出海码头取梁、载梁海上航行、抛锚定位、墩顶布置及落梁、专用运架船退出返回、箱梁精确就位(图11、12)。
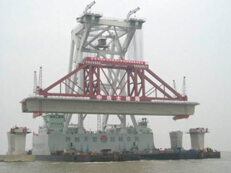
图11“小天鹅”号运架船
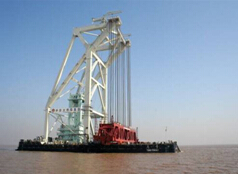
图12“天一号”号运架船
2)滩涂区大吨位整体预制箱梁运架
箱梁搬运包括从制梁台座至存梁台座和从存梁台座至提梁站的场内搬运、箱梁由地面上至桥面的垂直提升和箱梁在桥上长距离运输等,由于条件不同采用不同的运输方案:A)场内运梁采用两台800t搬运机联合搬运箱梁,该设备为轮胎式搬运机(图13);B)箱梁提升上桥采用两台吊重800t轮轨式提梁机原地将箱梁从地面提升到桥面(图14);C)箱梁梁上运输设备采用TE1600型轮胎车运输箱梁(图15);D)箱梁架设采用1600t步履式架桥机架设(图16)。
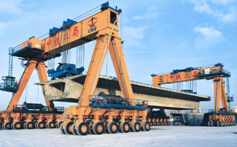
图13 ML800t轮胎搬运机
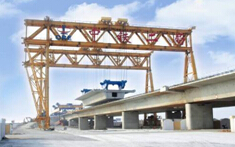
图14 HM800t提梁机

图15 TE1600轮胎式运梁车

图16 LGB1600t步履式架桥机
3)海上非通航孔桥预制墩身安装
预制墩身最大重量440.1T,对应高度17.383m。高度10.6米以下、重300T以下的墩身,选择苏连海起重8#作为安装船,该船长58.86m,宽27m;当墩身高度超过10.6米、重量大于300T时,墩身安装选择最大起重能力为500T的全旋转扒杆起重船。
为了便于墩身的安装与吊装,对定位支座、吊具及墩顶人孔进行了特殊设计。墩身安装过程解决了三个关键技术问题:A)墩身扭转。B)墩身临时固定。C)安装精度控制。D)湿接头施工质量控制。见图17。
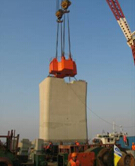
图17 预制墩身吊安
4)超长螺旋焊缝钢管桩沉桩
水中区引桥单幅桥钢管桩基础设计为9-12根Φ1.5m/1.6m桩,呈梅花型布置,桩最大斜率6:1。在杭州湾恶劣的风、浪、流条件下,大直径、超长钢管桩的施工关键取决于设备。本工程前后共投入7艘打桩船,所有船都配备有GPS全球卫星定位系统和大能量的液压锤或柴油锤。其中海力801#(图18)和天威号(图19)两条船的船型、配备、功能相近,是目前中国最先进的多功能全旋转式起重打桩船,其性能如表1所列。

图18 “海力801#”打桩船

图19 “天威号”打桩船
从2003年11月14日施打第一根钢管桩,平均月沉桩近260根,工期比原计划提前一年多。
(3) 结构耐久性保障技术
根据调查,影响本工程混凝土结构耐久性的主导因素是Clˉ(氯离子)的侵蚀。为此,针对本工程混凝土结构的不同部位,提出了混凝土结构耐久性多层次综合保障措施。
1)通过限制氯离子扩散系数和设置理的钢筋保护层, 作为保证大桥钢筋混凝土结构100 年设计使用年限的基本措施。采用的海工耐久混凝土, 主要以氯离子扩散系数为控制参数, 在原材料选方面, 主要考虑使混凝土具备高抗氯离子扩散能、高抗裂性能、高工作性能。
2)根据不同的情况和环境采用混凝结构表面防腐涂装、预应力筋保护、渗透性控制模、局部使用环氧钢筋和阻锈剂等附加措施。在斜拉桥索塔承台、塔座和浪溅区的下塔柱采用外加电流阴极保护技术。
3)设置预埋式耐久性监测系统, 用于长期动态获取耐久性参数, 制定本工程相应的耐久性预案。
4)建立耐久性暴露试验站, 对所采用的措施进行验证和参数校核。
(4) 运行安全控制技术
1)各种灾害性天气对大桥行车安全的影响分析,查明大桥有效运营通车总天数;
2)研究提高大桥通行运营服务水平的工程措施及管理措施,以及相应的经济指标;
3)提出大桥行车安全保障体系方案。
提出了:护栏由原设计高度1.2m增加为1.5m,护栏横梁间距考虑了风障功能;在航道桥及高墩区区段在护栏上增设变高度风障;为增加雾天行车安全性,;两侧护栏按路灯间距增设雾灯等多项工程措施。
(5) 宽滩涂区浅层气施工控制技术
在桥址南岸滩涂段初勘过程中发现有浅层气存在,其中CZK30孔浅层天然气喷发强烈,造成钻探船只倾覆沉没。开展了:A)浅层气成因分析;B)浅层气影响分析;C)浅层气工程对策分析及实施效果。
1)浅层气对打入桩施工影响小、对钻孔桩施工影响较大,施工必须采取必要措施;
2)预防浅层气对桩基施工与承载性能不利影响的有效措施是采取积极主动的控制放气;
3)针对6个区段,9个放气点气藏类型,在借鉴中国多个气藏开发技术基础上,提出了不同的放气技术方案和工艺流程。放气位置选定为距桥轴线上下游各20m,每个墩位布置两个排气孔。采用有控制性放气,并在基础施工开始前三个月进行。
4、主要技术特点和创新点
(1)工程特点
1)工程规模大、海上工程量大
2)自然环境恶劣、制约因素多
自然环境可概括为:潮差大、流速急、流向乱、波浪高、冲刷深、软弱地层厚,部分区段浅层气富集。据现场施工统计,海上施工作业年有效天数不足180天,滩涂区约250天。
3)设计要求新、施工难题多
大桥工程施工环境恶劣、有效作业时间短,施工安全问题突出,制定总体设计方案难度很大。设计上面对着如何满足耐久性要求、如何处理好结构与周边环境的协调、如何保障桥面行车安全等诸多新问题。在施工技术方面,面临着海上激流区高墩区大吨位箱梁的整体预制、运输及架设,宽滩涂区大吨位箱梁的长距离梁上运梁及架设,超长超重螺旋钢管桩的设计、整体制造及防腐与沉桩施工等诸多施工技术难题的挑战。
(2)创新点
工程实践证明,大桥所遵循的设计原则和采用的总体方案,充分利用了当代桥梁建设的先进技术手段,最大限度地减少了海上作业,符合海上工程的实际情况,对回避施工风险、保证施工安全、保证工程质量、缩短建设周期和降低工程造价发挥了重大作用,总体设计在实施过程中未发生过方案性变更。工程在实施过程中,主要实现了以下突破:
1)大桥全长36km,其长度在目前世界上在建和己建的跨海大桥中位居第一。
2)大桥地处强腐蚀海洋环境,国内首次采用100年的设计基准期,研发了以抵抗氯离子侵蚀为主的海工耐久混凝土。
3)大桥50m箱梁“梁上运架设”技术,架设运输重量从900t提高到1430t,刷新了目前世界上同类技术、同类地形地貌桥梁建设“梁上运架设”的新纪录。
4)大桥深海区上部结构采用70m预应力砼箱梁整体预制和海上运架技术,为解决大型砼箱梁早期开裂的工程难题,提出并实施了“二次张拉技术”。
5)大桥钢管桩的最大直径1.6m,单桩最大长度89m,最大重量73t,开创了国内外大直径超长整桩螺旋桥梁钢管桩工程之最。
6)首次在浅层气富集区建设大型桥梁,开创性地采用有控制放气的安全施工工艺,并形成了成套施工工艺。
5、有关资料
桥 名:杭州湾跨海大桥
桥 型:北航道桥双塔双索面五跨连续钢箱梁斜拉桥
南航道桥为独塔双索面三跨连续钢箱梁斜拉桥
跨 径:北航道桥主跨448m
南航道桥主跨318m
桥 址:杭州湾
建设单位:杭州湾大桥工程指挥部
设计单位:中交公路规划设计院(总体设计及第一合同段设计)
中铁大桥勘测设计院&中交第三航务工程勘察设计院联合体
(第二设计合同段设计)
北京交科公路勘察设计研究院
施工单位:中交第二航务工程局有限公司等
中铁大桥工程局有限公司
路桥建设股份有限公司
广东省长大公路工程有限公司
中铁第四工程局有限公司
中铁第二工程局有限公司
浙江省交工集团有限公司
宁波市交工集团有限公司等
钢材用量:80万吨
混凝土用量:245万立方米
造价:118亿元